
Laser Cutting Process
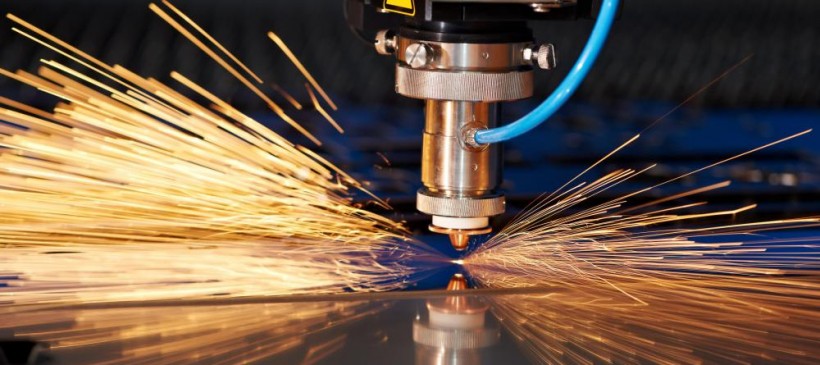
The laser cutting focuses on the output of the high-powered laser to engrave or cut materials like metal, wood, plastics, and many more. The area of specialization for USA Contract Manufacturing Specialists is steel laser cutting.
The technique is predominantly used for industrial manufacturing even though it is becoming more widespread in other industries and also schools. Laser cutting is an effective way to cut and engrave metallic materials even though it has its own set of challenges.
It is good to understand that lasers aren’t the answer to all the applications. However, the laser cutting process provides efficient use of materials, flexibility, and a controlled and repeatable process.
One key benefit of the laser cutting process over the other techniques like punching and stumping is the ability to work with minimal contact.
The typical cut width of 0.010 inches allows the laser cutters to be used in small-radius cutting. The small kerf supports close nesting of parts and assists in minimizing the waste of materials.
In addition, you can heat treat the materials after the cut with no distortions. Unlike the traditional cutting methods, you will not require any reforming and grinding after laser cutting.
Material Considerations
The laser cutting process becomes less effective when you increase the thickness of the material. For example, lasers can become ineffective when cutting carbon steel that is thicker than 4 inches. The limitations of laser cutting thickness are determined by the heat conductivity, vaporization point of alloys, surface reflection at 10.6 microns, part geometry, molten materials’ surface tension, and the types of alloys. As the thickness increases, there is a likelihood of thermal runaway or blowout also increases.
Laser becomes a sharper cutting tool by focusing its beam highly and reducing the spot size. For example, the cutting ability of laser significantly increases when you narrow the spot size from even .004 to .011 inches of diameter. The wavelength will ideally allow 100% absorbability with the material. In most cases, you can further increase the cutting ability of the laser by focusing the assist gas. The purpose of the assist gas is to blow the molten metal or debris away and help in the combustion.
If the thermal conductivity is so high in materials like aluminum, most of the energy will be transferred laterally into the materials, and this results in an inefficient cut and reduces the cutting speeds. The gas is transferred in the material inefficiently hence reducing the effectiveness of the laser cutting process. During the laser cutting process, certain metal amounts become molten or vapor. The laser cuts like the plasma cutter when processing thick materials or when you are melting large amounts of materials.
Part Geometry
The thermal process affects certain part geometries more than the others. For example, smaller or corner areas of the part absorb more heat which increases the probability of violent reactions and runaways. It is harder to maintain a more constant cutting speed when part geometry is more complicates. In most cases, productivity and speed are compromised when you are cutting shapes that have varying angles and curves. Generally, it is more efficient to speed up lasers while cutting curves to prevent deteriorating edge quality and part overheating. Pulsing the laser and not using a continuous wave to drill or pop holes is a technique that is used to avoid thermal problems.
Material Composition and Quality
The composition of the material affects the laser cutting process more dramatically than any other processing method. The laser process is affected by the viscosity and conductivity of metal in the liquid state. The surface tension for liquid metals influences the degree of dross that adheres to the part’s exit edge. The dross clings on the material and normally elevates the parts’ temperature. In such instances, you may require a second operation to remove the recast.
The carbon content helps in combustion making the materials combust quickly once they come into contact with the laser beam. Random reactions can occur during the thermal process because of the surface condition of the material and its element variance. The surface condition entails surface impurities, filth, coatings, and scale. Sometimes, the dwelling process is used in cutting materials that are particularly reflective like aluminum. The laser may dwell in the starting position until the reflectivity of the material changes or before the motion systems start to move the laser.
The other things that affect the performance of the laser are the carbon content, surface tension, and absorbability of the material at 10.6 microns. For instance, it is very difficult to cut the copper material due to its reflectivity but this is not the case when using the other cutting methods.
Material Quality
The laser cutting process is more sensitive to the quality of material more than any other type of process. The finish of the surface significantly affects the cutting quality. In most cases, the steel material must be oil-free, pickled, and clean. Having impurities on low-grade steel makes is highly reactive to the thermal process especially when your processing gas is oxygen. Hot rolled steel also presents several quality problems during the cutting because of the surface scale. The surface will melt in with the metal hence creating an undesirable finish. If the surface of the material isn’t smooth, the laser focus and gas can get altered hence affecting the quality of the cut.
Laser cutting may leave a recast layer on the metal surface. The lasers burn and melt some of the metal and the re-melted materials are deposited on the sides of the cutting edges and on the cut bottom. The layer of these deposited materials may crack because it is highly stressed more so if it is an oxide. Even though these are small cracks, they may propagate in the material and create large cracks. This is specifically true for inside corners with small radii that are characterized by higher stresses. High-pressure nitrogen cutting can eliminate these cracks in certain cases. For instance, titanium is highly reactive to oxygen. Thus, oxygen embrittlement may result in micro-cracks which is a significant safety concern for titanium users like the aerospace industry. In this case, avoiding fatigue and long-term cracks are so critical. The solution is the use of high-pressure nitrogen. The technique turns the lasers into controlled welding equipment by blowing away the molten materials with 160 PSI (pounds per square inch) gas.
High-power nitrogen cutting is highly expensive and consumes a lot of time. The reason is that you have to control its motion system precisely. However, high nitrogen cutting delivers high cutting speeds. Currently, this cutting method is utilized on 300 series of stainless steel.
When you plan similar laser cutting jobs to run together, you can also reduce the setup time significantly. The other tips include keeping the material close to the laser cutting table, using shuttle tables, building ergonomic workstations, creating modular fixtures among others. You can also increase efficiency by the use of delivery optics that can be changed quickly, indicating procedures, and eliminating alignment. Reputable brands like USA Contract Manufacturing Specialists use these tips to make the laser cutting process a success.
Setup Time
The set-up time for the laser cutting process can be so long when you are preparing to cut unfamiliar metals. Some of the factors that influence the process include focal length, speed, gas pressure, assist gas, optical focal length, and nozzle power. These parameters are so crucial to the process such that if you fail to set them correctly, you won’t be able to cut the material. However, with the correct combinations, the cutting speed can be several times faster than the other cutting methods.
You can reduce the setup time using several methods. First, you must keep meticulous methods. You must also use a reliable database of time-tested parameters for known conditions, specifications, and materials. The parameters for the same materials are often wide-ranging. The requirements for flatness, heat-affected zone, tolerances, and surface finish can change the parameters significantly.
If you need any of our services, feel free to get to us and we will give you a free quotation. The company guarantees you that you will get the value for your money in any service that you hire from us. We have the right technicians and machines to help you out on any metal project that you could be having at your individual or business needs.